1. Optimal Trajectory Generation for Precision Motion Systems
The objective is to develop optimal trajectory generation algorithms for high speed high precision motion systems such as machine tools or industrial robots.
Reference trajectory carries great importance for the overall positioning accuracy of the motion system. We are trying to optimize kinematics of the reference trajectory with respect to several metrics such as residual vibrations, total machining cycle time, actuator limits and energy consumption. The key application is 5-axis machining.
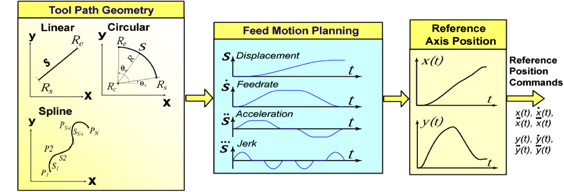
2. Controller Design for Multi-axis Coordinated Motion
Motion synchronisation is a well-known problem that occur in coordinated multi-axis motion. Synchronisation is mainly dictated by the reference tool-path. However, due to dynamics mismatch and external disturbances it cannot be always preserved during cutting operation. The objective is to design contouring controller for modern machine tools so that precision path following is achieved at higher speed under cutting disturbances.
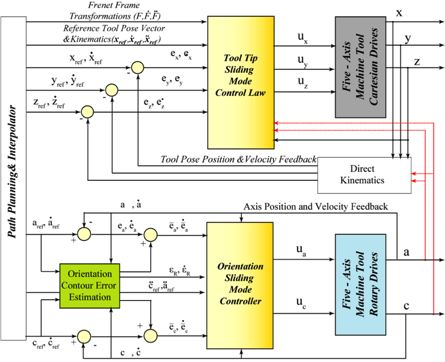
3. Machining Process Optimization
Metal cutting processes are heavily utilized in generating the final shapes of the parts. The research objectives here is to model kinematics and dynamics of metal cutting operations and optimize cutting parameters for better productivity. Our objective is to incorporate machine dynamics to find optimal feed direction and cutter orientation to achieve stable and precise cutting.
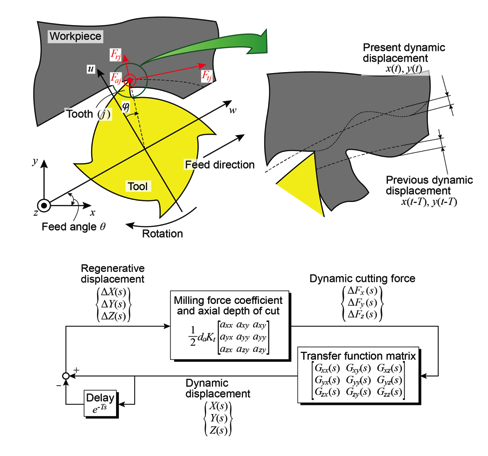
The objective is to develop optimal trajectory generation algorithms for high speed high precision motion systems such as machine tools or industrial robots.
Reference trajectory carries great importance for the overall positioning accuracy of the motion system. We are trying to optimize kinematics of the reference trajectory with respect to several metrics such as residual vibrations, total machining cycle time, actuator limits and energy consumption. The key application is 5-axis machining.
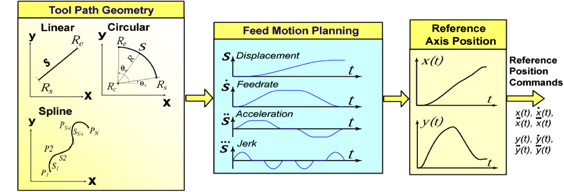
2. Controller Design for Multi-axis Coordinated Motion
Motion synchronisation is a well-known problem that occur in coordinated multi-axis motion. Synchronisation is mainly dictated by the reference tool-path. However, due to dynamics mismatch and external disturbances it cannot be always preserved during cutting operation. The objective is to design contouring controller for modern machine tools so that precision path following is achieved at higher speed under cutting disturbances.
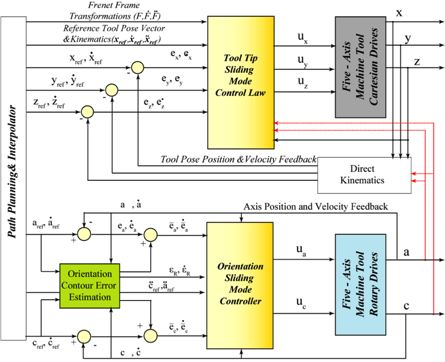
3. Machining Process Optimization
Metal cutting processes are heavily utilized in generating the final shapes of the parts. The research objectives here is to model kinematics and dynamics of metal cutting operations and optimize cutting parameters for better productivity. Our objective is to incorporate machine dynamics to find optimal feed direction and cutter orientation to achieve stable and precise cutting.
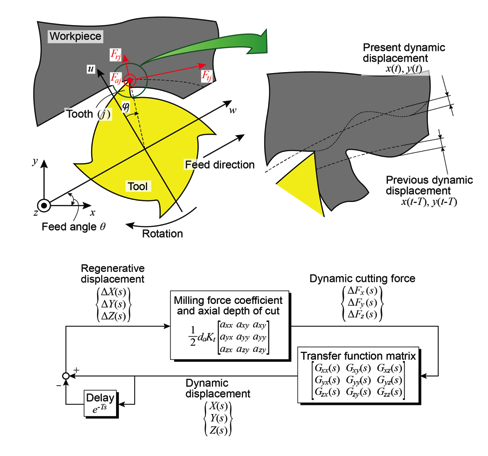