Each year approximately 10 billion tons of concrete is produced, making concrete the largest manufactured product globally. The majority of this production is in the form of ready mix concrete. In the United States alone, there are about 5,500 ready mix concrete plants and about 55,000 ready mixed concrete mixer trucks that deliver concrete to the point of placement. The quality control (QC) and quality assurance (QA) of this large operation have major economic, social and environmental implications. Construction projects using ready mix concrete require strict adherence to the established standards for specifying, ordering, mixing, delivering and curing, such as those defined by ASTM C94, the Standard Specification for Ready-Mixed Concrete. Despite all efforts and streamlined procedures, many newly constructed structures suffer from performance and long-term durability problems due to low-quality concrete.
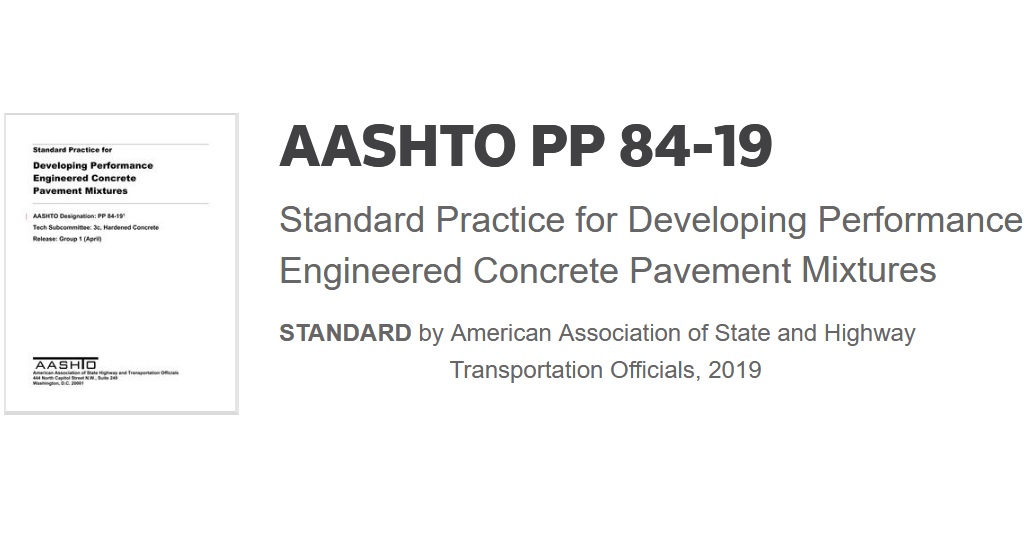
Construction specifications are a series of instructions provided by an owner (e.g., a state highway agency) to a contractor/producer that describes the materials and processes that are to be used for a project. Recently, a conceptual specification has been provisionally approved by the American Association of State Highway and Transportation Officials (AASHTO) for use in concrete pavements with potential extension to concrete bridge decks. Unlike traditional workability and strength based specifications, this new specification also deals with issues of salt damage, freeze-thaw, corrosion and volume change.
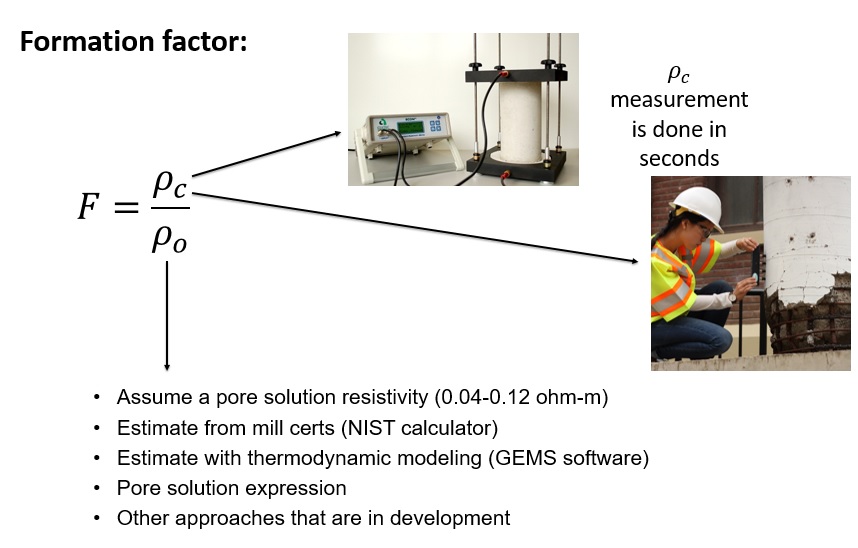
This new approach for specifying and assessing concrete uses electrical-based methods. As we use compressive strength as a performance index to specify/assess mechanical properties of concrete, we can use electrical properties of concrete to specify/assess durability performance. Formation factor is a critical electrical property of concrete that can be used as a performance index for concrete durability.